News
News
- What is a sacrificial anode
- Basic requirements for reference...
- What does the reference electrode do...
- Why are zinc blocks attached to the ...
- What is the principle of impressed...
- What material does metal structure...
Contact
Phone:18739187123
hotline:0391-7588881
E-mail:970512272@qq.com
Address:Wuzhi County, Jiaozuo City, China
Q & A
What are the ways to prevent metal corrosion?
- Author:Libo
- Source:wphotodu.cn
- Date:2021-08-10
- Click:0
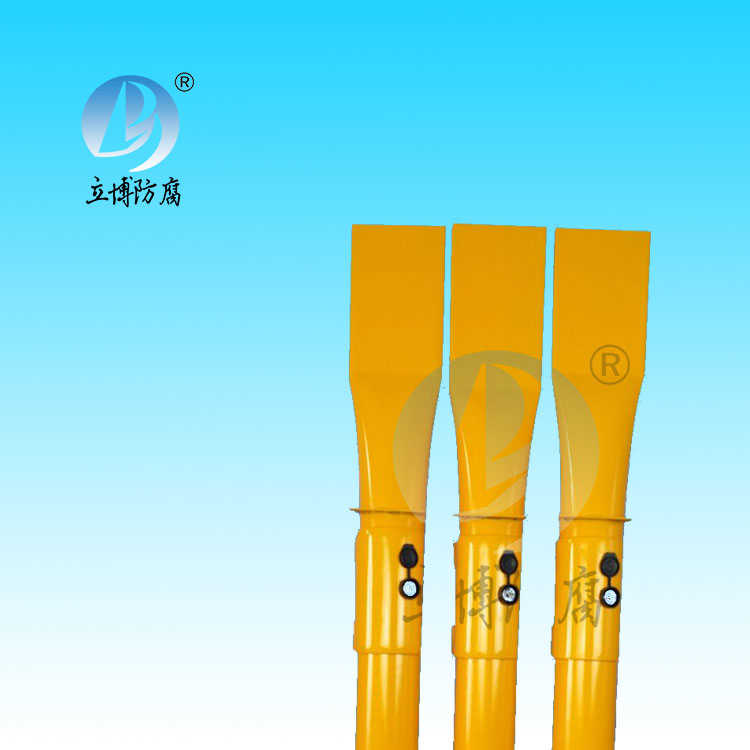
(1) Non-metallic protective layer. The corrosion resistant non-metallic substances, such as paint, spray paint, enamel, ceramics, glass, asphalt, polymer materials (such as plastic, rubber, polyester), etc., are coated on the metal surface to be protected, so that the metal is isolated from the corrosive medium.
(2) Metal protective layer. Cover the protected metal surface with a strong corrosion-resistant metal or alloy by electroplating, hot spray plating, vacuum plating and so on. According to the electrochemical properties of corrosion protection, the protective layer can be divided into anodic protective layer and cathodic protective layer. The standard electrode potential of the anode protective metal is lower than that of the base metal, such as galvanized iron plate, with zinc as the anode and iron as the cathode. The standard electrode potential of the cathodic protective metal is higher than that of the base metal, such as tin plating, with tin as the cathode and iron as the anode. There is no principle difference between the two layers as far as the protective layer separates the metal from the environment. But when the protective layer becomes damaged and incomplete, the situation is different. As mentioned earlier, the cathodic protection layer will cause the base metal to become an anode, resulting in pitting. An anodic protective layer, such as a galvanized iron plate, in which zinc is the anode and the base metal iron is the cathode, is corroded by zinc plating, not iron. Corrosion of the base metal does not begin until the coating is sufficiently damaged to provide protection against the base metal.
(3) Electrochemical protection.
(1) Sacrificial anode protection: connect the metal with a lower standard electrode potential and the metal to be protected to form a battery. At this time, the metal that needs to be protected becomes the cathode due to the higher electrode potential and is protected from corrosion. Another metal with a lower electrode potential is the anode, which is corroded. For example, at sea, ships have pieces of zinc around their bottoms. In this case, the hull is the cathode, which is protected, and the zinc block is the anode, which is corroded instead of the hull. This protection law protects the cathode while sacrificing the anode, so it is called sacrificial anode protection law.
(2) Cathodic protection: this is the use of external power supply to protect the metal. The metal to be protected is connected to the negative electrode to make the cathode free from corrosion. Take some iron and attach it to the positive pole, make it an anode, make it corrode, and actually sacrifice the anode. Unlike the previous method, the current is supplied by an external source, rather than by the battery itself. Chemical plants in some acidic solution storage tank or pipeline, as well as underground water pipes, pipelines, etc., commonly used in this method corrosion prevention.
Anode protection: this is also the use of external DC power supply to protect the metal. But the metal to be protected is connected to the positive pole to make the anode. Supposedly, this should accelerate metal corrosion. But for some metals that can form a protective oxide film, it does not necessarily accelerate metal corrosion. On the contrary, in an appropriate positive potential range, due to the intensification of oxidation on the anode, a complete oxide film is formed on the metal surface, so that the metal is protected and the corrosion current decreases significantly. This phenomenon is called the electrochemical passivation of metals. Anodic protection is to passivate the metal under the action of an external anodic current, so that it is passivated and protected.
(4) Add corrosion inhibitor to protect.
A corrosion inhibitor is a chemical substance that, when added in small amounts to a corrosive medium, can significantly reduce the rate of corrosion of a metal. Because the amount of corrosion inhibitor is small, simple and economic, so it is a common means of corrosion prevention. Corrosion inhibitors generally fall into three categories.
Passivating agent: generally inorganic strong oxidant. For example, chromate, nitrate, molybdate, etc. Their function is to make the corrosive medium has a stronger oxidation, so that the metal surface to maintain a complete oxide film. Its function is similar to the anodic protection of electrochemistry.
(2) Organic corrosion inhibitors: including acid pickling corrosion inhibitors and corrosion resistant oils. Pickling of steel is an essential pretreatment process for many processing processes, the purpose of which is to remove oxides from the surface of steel, but this process inevitably leads to corrosion of the metal itself. In order to reduce the corrosion of metals, corrosion inhibitors must be added during pickling. This corrosion inhibitor is usually: o and para toluene thiourea, propyl thioether, diamyl amine, formaldehyde, para thiocresol and so on. The mechanism of action is that the corrosion inhibitor is generally adsorbed on the surface of steel, which makes the electrode reaction that causes corrosion in steel pickling hindered. Some corrosion inhibitors can increase the overvoltage of hydrogen, so that the cathode reaction of hydrogen ion reduction is blocked. Some corrosion inhibitors can inhibit the oxidation of iron to ferrous ion and make the anode polarized. However, it is generally believed that corrosion inhibitors can slow down the cathodic and anodic reactions at the same time, so that the corrosion rate of steel is significantly reduced.
Anti-corrosion grease is used for temporary corrosion protection of metal materials and parts during transportation and storage. It is mainly composed of oil, grease or wax with a small amount of organic additives. These organic additives are generally polar compounds that can be adsorbed to metal surfaces. Its mechanism of action is similar to that of acid pickling inhibitor, except that the additive in the anti-corrosion oil is required to act under near-neutral conditions, while the acid pickling inhibitor is required to act under acidic conditions. Organic substances commonly used as additives in resist oils and fats are: organic amines, zinc naphthenate, oxidation products of various petroleum products, alkali metals of sulfonated oils and salts of alkali earth metals.
(3) gas phase corrosion inhibitor: gas phase corrosion inhibitor is a kind of volatile, but the vapor pressure is low and its vapor has the anti-corrosion effect of the substance. It is mainly used for anticorrosion of important machine parts (such as bearings, etc.) during storage and transportation. Its anti-corrosion mechanism is not very clear, mainly the adsorption of gas phase inhibitor on the metal surface. The most effective and the most widely used gas phase corrosion inhibitor is nitrite bicyclohexylamine, which is a non-toxic and odorless white crystal, volatilization is slow, in a good closed packaging space, room temperature can have a year of effective corrosion of steel parts. Its disadvantage is that it will accelerate the corrosion of some non-ferrous metals such as zinc, manganese, cadmium and so on, so special attention should be paid to whether there are non-ferrous metals in the parts when used.